
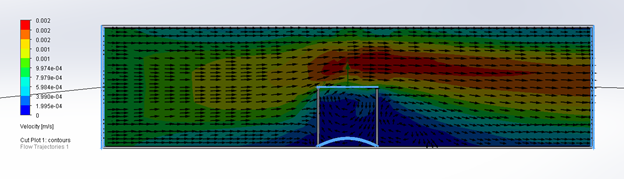
In other words, the solver continues to iterate until the values of the goals flatten off, indicating that the system has reached steady-state equilibrium. In the case of steady-state analysis, the convergence of goals is tracked and utilized as a stopping criteria for the solver. Key parameters of interest are tracked during the solution by the creation of user-defined goals.
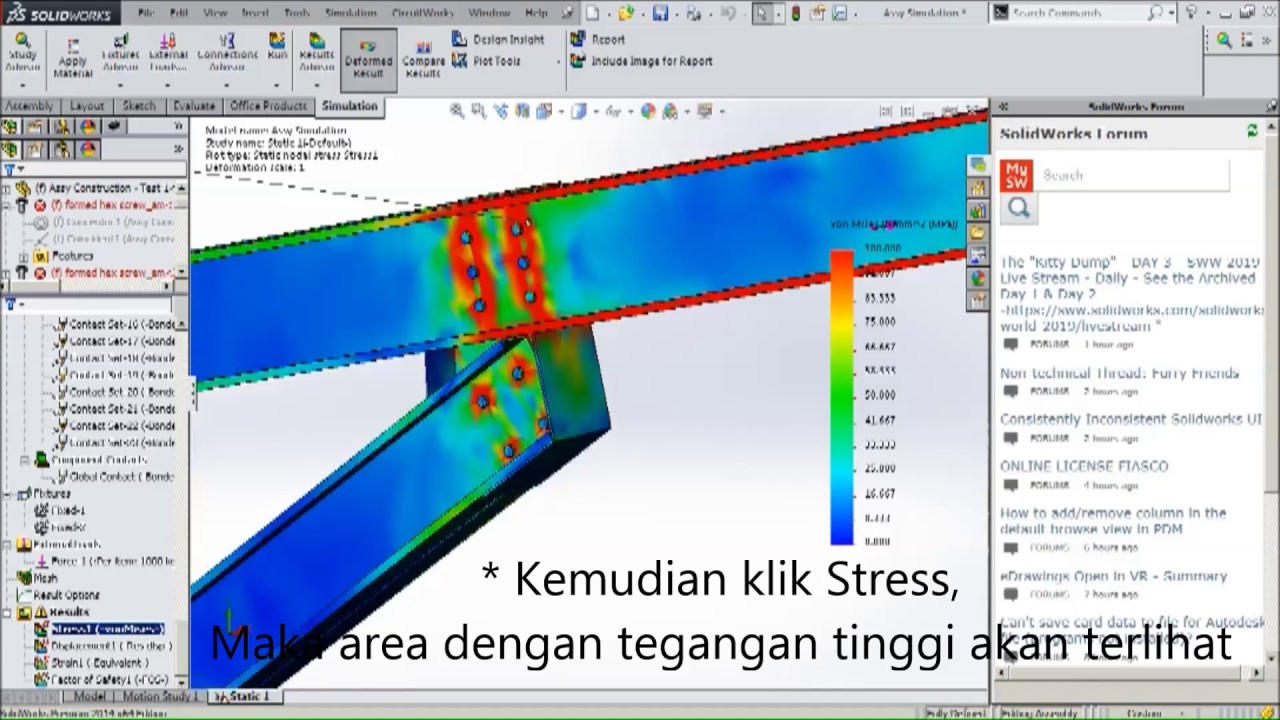
The computational domain is broken up into a Cartesian mesh, a grid-like mesh made up of box-shaped cells, which will be discussed later in this article. Background & Terminologyįlow Simulation is a computational fluid dynamics (CFD) analysis package using the finite volume method. This article will examine the use cases of SOLIDWORKS Flow Simulation as it relates to thermal analysis, with a specific focus on predicting the performance of electronics cooling systems. The ability to simulate heat conduction combined with convective heat transfer generated by airflow over heatsinks and chip packages offers a high degree of confidence in temperatures predicted, especially when compared to traditional hand calculations or FEA-based thermal analysis where assumptions about airflow must be input in the form of convection coefficients. One of the most common applications of Flow Simulation today though is thermal analysis for predicting cooling performance of electronics and other heat generating components. Because it is a general-purpose fluid dynamics analysis package, Flow Simulation can analyze a wide variety of problems, including: aerodynamic and hydrodynamic problems such as pump and propeller design, head loss in piping systems and coefficient of drag calculations for vehicles. SOLIDWORKS Flow Simulation is a powerful, general-purpose CFD package integrated directly into the SOLIDWORKS CAD environment.
